Operations Excellence
“Focus on the Process”
Operation Management
“Operations management is the administration of business practices to cre− ate the highest level of efficiency possible within an organization.
Operations management is concerned with converting materials and labor into goods and services as efficiently as possible.
Corporate operations management professionals try to balance costs with revenue to maximize net operating profit.”
Full Operations Potential
We help our clients design a coherent vision of the operations system, implement road map and a change management strategy.
This will move forward as we engage all levels of the organization in execution to create ownership.
Process upgrades: The company will adapt a specific process to support an integrated operations agenda and ensure the corporate business
functions, from business strategy to human resources to digital and analytics, are operationally focused.
We deploy across the enterprise a full capability-building strategy that spans functional capabilities and transformation skills. We develop a change management process to achieve engagement and change mindset.

Operational Exellence
An enterprise is on the right path to Operations Excellence (OE) when “Each and every employee can see the flow of value to the customer and fix that flow before it breaks down”.
Based on well known assessment scheme enables companies to get a quick assessment of their operations performance. This assessment will define 15 areas of operations assessing the current state and to plan the future state of enterprise operations. It has been successfully applied in several enter− prise reengineering projects to provide decision-makers with sufficient input to identify improvement targets and revise the current operations strategy.
Move on to Excellence
-Customer satisfaction: From no measurement and understanding of customer satisfaction to fully displayed ratings and interactive, cross-functional involvement at all levels.
– Leading technology: From low awareness to full awareness and utilization of leading technology to provide a competitive advantage
– Safety, environment, cleanliness and order: From untidy to 100% organized, 100% of the time
-Visual management deployment: From informal, infrequent, and fragmented, to 100% updated and 100% visualized information about objectives, status and
-Manufacturing planning and control system: From poor delivery performance often with high inventory, to excellent performance in delivery, quality, cost, and schedules being achieved 100% of the time
-Order management: From functionally oriented, manual, and cumbersome, to customer-oriented, responsive, and automated order management
-Information system: From low awareness of the potential of IT to computer integrated and enabled
-Layout, product flow, space use & material movement means: From functional to 100% interconnected and flow- oriented layout
-Levels of inventory and work-in-progress: From no recognition of the waste of overproduction to mixed model production with low inventory and high customer
-Team work, skill levels and motivation: From strict hierarchy to a highly empowered, flexible and team based organization
-Condition and maintenance of equipment and tools: From no maintenance, or expert maintenance, to full participative TPM
-Quick changeover: From belief that the way to reduce total set up time is via increased batch size to full SMED
-Value chain integration: From adversarial, guarded to full partnership with information sharing and value chain co-operation.
-Commonality of routines, equipment and components: From complex, varied and unspecified, to simple and 100% standardized
-Quality system deployment: From supervisors being responsible for inspections to TQM based on process control, prevention, operator responsibility
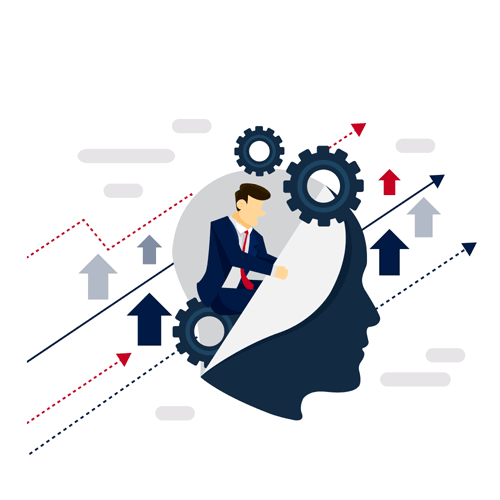
Business Applications
- Operations
- Manufacturing
- Customer Care
- Human Capital &
- Talent Management
- Supply Chain
- Material Management
Deliverables
-Audit Results: This will deliver a support the management in the assessment of operations performance.
-Gap Analysis: Based on the audit results we analyze the gap between those results and the requirement of Opera− tion
-Target Setting: Prioritizing the targets of opportunities for improvement
